Zehn tolle Lösungen
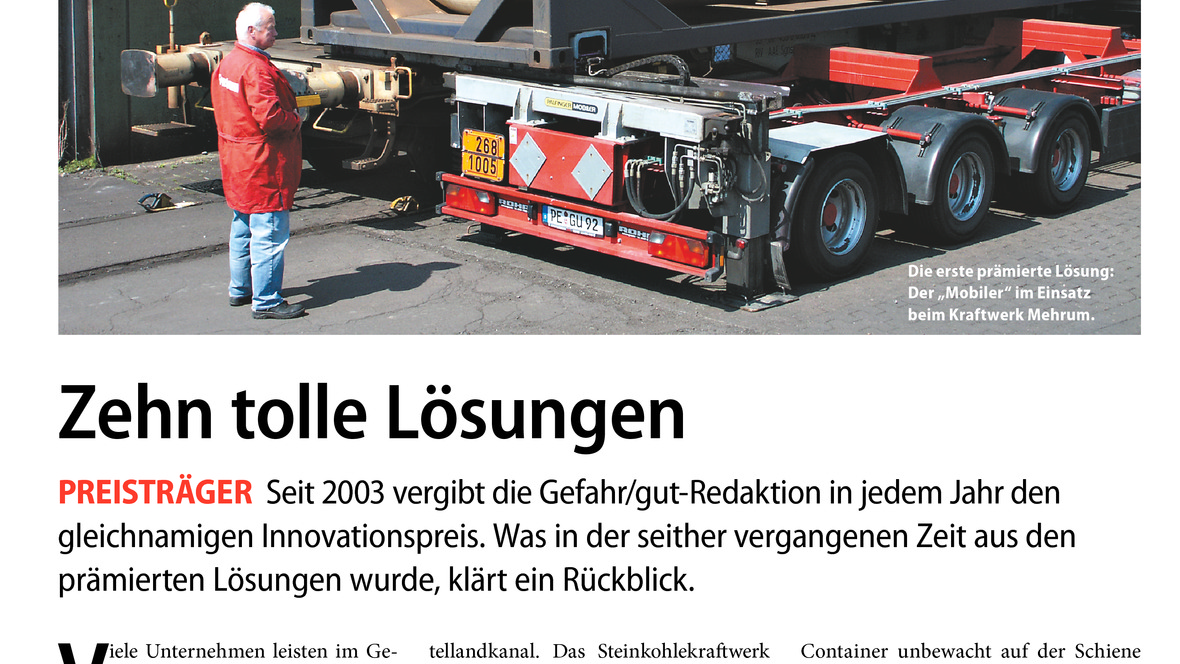
© Gefahr/gut
Viele Unternehmen leisten im Gefahrgutbereich hervorragende Arbeit. Mit innovativen Lösungen sorgen sie dafür, dass die Sicherheit bei der Beförderung von und im Umgang mit gefährlichen Gütern gewährleistet und ständig verbessert wird.
Seit mittlerweile zehn Jahren honoriert die Redaktion der Gefahr/gut diese Bemühungen mit der Verleihung des Innovationspreises Gefahr/gut. Jahr für Jahr wählt der Fachbeirat der Zeitschrift (siehe Kasten auf S. 22) aus den Bewerbern ein Unternehmen aus, das eine innovative Gefahrgutlösung eingeführt hat, und kürt es zum Sieger des Wettbewerbs (siehe Kasten auf S. 23).
Zum ersten Mal ging der Preis im Jahre 2003 an das Kraftwerk Mehrum am Mittellandkanal. Das Steinkohlekraftwerk hatte sich beworben mit der Vorschubtraverse „Mobiler“ des Herstellers Palfinger, die die Anlieferung von Ammoniak-Tankcontainern für die Rauchgasentstickung sicherer gestaltete. Mit Hilfe dieser Traverse, die auf einem Sattelauflieger montiert war, konnten die Container direkt vom Bahn-Tragwagen auf den daneben wartenden LKW-Trailer verschoben werden. Dies verringerte die Strecke, die der Gefahrguttransport auf der Straße zurücklegen musste, auf den Weg vom nächsten Anschlussgleis bis zum Unternehmen.
Da die Bahn inzwischen viele Gleisanschlüsse aufgehoben hat, werden die Ammoniakbehälter für Mehrum heute im Terminal Hannover auf den LKW verladen. Zudem ist so garantiert, dass kein Container unbewacht auf der Schiene steht. „Wir hatten den Mobiler aber noch bis vorletztes Jahr voll im Einsatz“, erinnert sich Bernhard Michels, damals wie heute Geschäftsführer des Kraftwerks. Und bis zum heutigen Tag steht das Gerät für den Fall der Fälle bereit: „Wenn ein Container ausnahmsweise von einer anderen Anschlussstelle zu uns gebracht werden muss, ist der Mobiler unsere Backup-Lösung“, sagt Michels.
Datenbank gegen Missbrauch
Im ADR 2005 wurden mit Kapitel 1.10 erstmals Vorschriften für die Sicherung gefährlicher Güter gegen missbräuchlichen Zugriff aufgenommen. Die Spedition Lechner in Parsdorf bei München griff dieser Regelung voraus und bewarb sich schon 2004 mit einer Online-Datenbank, in der die Fotos der LKW-Fahrer hinterlegt wurden. Kunden des Spediteurs erhielten ein Passwort, mit dem sie sich in diese Datenbank einloggen und bei Einfahrt des Lasters in das Werksgelände kontrollieren konnten, ob der Fahrer auf dem Bock tatsächlich der richtige war. Firmenbescheinigungen und Sicherheitsausweise, die gerne vergessen wurden oder bei einem Fahrerwechsel neu ausgestellt werden mussten, konnten damit entfallen.
Das Interesse der chemischen Industrie an der prämierten Lösung war groß. „Wir hatten Besuch von großen Konzernen wie Wacker und BASF“, berichtet Ümit Sengüler, seinerzeit Gefahrgutbeauftragter bei Lechner und heute Mitarbeiter der Spedition Klaeser, die im Jahre 2011 die Spedition Lechner übernommen hatte. Die BASF, so ist von einem Sprecher des Unternehmens zu erfahren, hatte in Ludwigshafen daraufhin ein eigenes System zur Fahreridentifikation entwickelt.
Module für die Sicherung
Mehr Sicherheit, allerdings für die Ware auf der Ladefläche, war auch Ziel des Modulsystems „Cargo Safe“, für das die Bielefelder Sommer Fahrzeugbau 2005 den Innovationspreis erhalten hatte. Mit Hilfe eines ineinandergreifenden Systems von Lochprofilen, dem Sommer-Außenrahmen-Ladungssicherungssystem SALS, Schubklötzen, Sperrbalken, Trennwänden, Einsteckbrettern, Rungen und Seitenlatten konnten Stückgüter an jeder Position des LKW-Aufbaus gesichert werden.
Im Laufe der Zeit wurden die einzelnen Teile der Lösung weiter verbessert, verfeinert und leichter gemacht. „Alle Module sind immer noch lieferbar, auch nach dem Übergang auf Sommer in Laucha“, erklärt Gerhard Sommer, früher Mitinhaber und Geschäftsführer und inzwischen Berater der Nachfolgefirma Sommer, die die neuen Gesellschafter 2010 aus der in Konkurs gegangenen Sommer Fahrzeugbau erworben hatten. „Wir sind heute noch stolz auf den Preis“, bekräftigt Sommer und ergänzt: „Der Pokal steht nach wie vor auf meiner Fensterbank.“
Die Brandschutzvorschriften mit den wirtschaftlichen Anforderungen bei Bau und Betrieb eines Gefahrstofflagers zu kombinieren, ist eine anspruchsvolle Aufgabe. Der Stuttgarter Logistikdienstleister LSU Schäberle hat dieses Problem mit Hilfe einer so genannten Oxy-Reduct-Anlage gemeistert. Sie verringert den Sauerstoffgehalt der Luft im vollautomatischen Hochregallager, so dass ein Brand erst gar nicht entstehen kann. Für diese Lösung durfte der Spediteur den Innovationspreis 2006 in Empfang nehmen.
Die prämierte Anlage mit über 13.000 Palettenstellplätzen ist bis heute in Betrieb. „Wir haben lediglich das Energiemanagement verbessert, was uns eine Ersparnis von rund 20 Prozent gebracht hat“, weiß Geschäftsführer Thomas Schäberle und fährt fort: „Der Preis war die Krönung für ein auch heute noch außergewöhnliches Projekt eines Mittelständlers.“
Aus 1.4 mach 9
Wegen ihrer explosiven Natur sind Airbags beim Transport der Gefahrgutklasse 1.4 zuzuordnen. Zumindest wenn beim Verpacken nicht ein Produkt wie die „Fire-Box“ von Nordpack aus Isernhagen bei Hannover zum Einsatz kommt. Dank eines in diesen Wellpappekarton eingearbeiteten Metallgitters, mit dem die Verpackung den so genannten Bon-fire- oder 6c-Test bestanden hatte, konnten Airbags und Gurtstraffer gemäß den Bestimmungen für Klasse 9 befördert werden. Den Juroren war dies den Preis des Jahres 2007 wert.
„Das Produkt hat sich mittlerweile gut etabliert“, versichert Mark Dammeyer, Nordpack-Prokurist und Vertriebsleiter im Bereich Gefahrgut. Trotzdem entwickele man kontinuierlich weiter, da unterschiedliche Güter unterschiedliche Verpackungsformen verlangten. Das Grundprinzip basiere jedoch immer auf dem Metallgitter im Sandwichkarton. „Im Moment läuft eine Testserie für eine Ultra-Firebox“, berichtet Dammeyer, da die normale Firebox mit bestimmten Airbag-Modulen den 6c-Test nicht bestehe. Und weiter: „Wahrscheinlich werden wir Mitte des Jahres ein konkretes Ergebnis haben.“
Mängel bei diversen Gefahrgutlieferungen aus dem Fernen Osten waren Grund für Clariant, das E-Learning-Tool „Transport of Dangerous Goods by Sea“ zu entwickeln. Der Schweizer Chemiekonzern gewann damit den Preis im Jahre 2008.
Da das Programm bei Zulieferern wie Mitarbeitern gut ankam, folgten dem Erstling weitere Tools. Für einen großen Teil davon wurden laut Mitteilung des Unternehmens sogar mehrere Sprachversionen erstellt. „Die Verleihung des Innovationspreises hat sicherlich geholfen, dasss ein entsprechendes Budget zum Ausbau zur Verfügung gestellt wurde“, erklärt eine Clariant-Sprecherin.
Weniger Erfolg scheint dem Gewinner des Innovationspreises 2009 beschieden gewesen zu sein. Unter dem Namen „Pensatronic“ hatte CMP Container Master Projekt in Westertimke bei Bremen ein Achslastvermessungssystem für Nutzfahrzeuge mit Zwischenrahmen für Container entwickelt, mit dem auch das Gewicht flüssiger Ladung in Tankcontainern exakt bestimmt werden konnte. Ein offenbar leider kurzlebiges Projekt, da die Firma trotz intensiver Nachforschungen nicht mehr aufzufinden war.
Hinter sicheren Gittern
Gefährliche Stoffe sicher zu lagern, aber auch zu transportieren, ist besonders für kleine Unternehmen oft ein großes Problem. Die Firma CSS Cargo Safety Systems hatte deshalb eine Gitterbox mit festen Seitenwänden, einem verschließbaren Deckel, Belüftungsschlitzen, Staplertaschen und einer Auffangwanne ausgerüstet und sich im Jahre 2010 für den Innovationspreis beworben. Clou des Ganzen war eine von Hand verstellbare senkrecht stehende Platte im Inneren der Box, der „GiboMaxx“, mit dem nach jedem Be- und Entladevorgang die verbliebenen Fässer, Eimer und Kanister formschlüssig gesichert werden konnten. Auch die Jury war seinerzeit von der Preiswürdigkeit der „GoStore-Box“ überzeugt.
Die Gitterbox weckte schnell Interesse und wird auch heute noch geliefert – allerdings in überarbeiteter Form. „Wir verwenden jetzt nicht mehr den GiboMaxx, sondern das Lasifix-System, das können Sie sogar neigen und schräg stellen“, erklärt Dietmar Wichmann, Geschäftsführer der damaligen CSS wie auch der Nachfolgefirma CSI Cargo Safety Innovations. Darüber hinaus kann die GoStore-Box nun mit einem automatischen Löschsystem und RFID-Transpondern ausgerüstet werden. Eine Multifunktionsklappe komplettiert die Weiterentwicklungen.
Bevor Verpackungen aus Polyethylen für den Transport gefährlicher Güter zugelassen werden, müssen sie ausreichende chemische Werkstoffverträglichkeit beweisen. Mit einem Nachweis, der deutlich schneller und kostengünstiger als die bisherige Labormethode B ist und darüber hinaus stets reproduzierbare Ergebnisse zeigt, konnte der Darmstädter Chemiekonzern Merck den Sieg im Jahre 2011 davontragen. „Die Methode läuft weiterhin sehr stabil“, sagt Ralf Kranz, Leiter Prüfstelle Packmittel und Leiter Qualitätssicherung und Qualitätskontrolle bei Merck. Die Industrie zeige seither starkes Interesse, einige Unternehmen wollen die neue Methode ebenfalls einführen. „Und auch die Kunden merken, dass wir in Sachen Sicherheit eine sehr hohe Kompetenz haben, wenn wir ihnen sagen, dass wir den Innovationspreis Gefahr/gut gewonnen haben“, fasst Kranz zusammen.
Carbon macht stabil
Last but not least wurde im vergangenen Jahr der Straubinger Fahrzeugbauer Kurt Willig zum Preisträger gewählt. Unter dem Namen „BC+“ baut die Firma leichte und stabile Querträger aus Carbon in die Achsaggregate von Tankaufliegern. Dies erhöht nicht nur die Nutzlast, der kohlefaserverstärkte Kunststoff macht das Fahrzeug auch sicherer, da die beim Fahren auftretenden Kräfte bereits im Rahmen neutralisiert werden und sich nicht auf die Tankkonstruktion auswirken können.
In den Monaten seit der Preisverleihung ist der Anteil der Carbon-Fahrzeuge deutlich gestiegen. „70 Prozent unserer Sattelauflieger haben heute den Querträger aus Carbon“, meint Geschäftsführer Andreas Gillner. Generell ist für den Fahrzeugbauer die Verwendung von Kohlefaser ein zentrales Thema. „Und bis 2014 möchte ich eine Weiterentwicklung auf Carbonbasis im LKW-Unterbau vorstellen“, kündigt Gillner an.
Zehn Jahre, zehn Sieger, zehn Lösungen – und auch die Bewerbungen für den Innovationspreis Gefahr/gut 2013 klingen vielversprechend. Wer das Rennen gemacht hat, wird am Abend des 6. Mai anlässlich der 23. Münchner Gefahrgut-Tage verraten.
Rudolf Gebhardt
Die Jury
- Udo Binöder, Staub & Co.
- Bernhard Droste, BAM
- Herbert Gebhardt, TÜV Süd
- Claus-Dieter Helmke, DHL Freight
- Erwin Hollekamp, BASF Coatings
- Jörg Holzhäuser, Innenministerium Rheinland-Pfalz
- Ulf Inzelmann, Umco Umwelt Consult
- Ullrich Lück, Kombiverkehr
- Ulrich Podzuweit, FH München
- Michael Rannenberg, Universität Stuttgart
- Frank Rex, Polizei Niedersachsen
- Klaus Ridder, Gefahrgutexperte
- Helga Schmidt, VCI
- Michael Schuhmacher, Flughafen Düsseldorf
- Malte Stamer, Dekra
- RA Hans-Günter Triebel, Gefahrgutexperte
- Alfred Winklhofer, IHK Schwaben
Die Preisträger
- 2003 Kraftwerk Mehrum
- 2004 Spedition Hans Lechner
- 2005 Sommer Fahrzeugbau
- 2006 LSU Schäberle
- 2007 Nordpack
- 2008 Clariant
- 2009 Container Master Project
- 2010 Cargo Safety Systems
- 2011 Merck
- 2012 Willig
© Copyright 2025 Gefahrgut-Online
Diskutieren Sie mit